What Dyndrite’s New API Toolsets Mean to Machine OEMs and Developers in the Additive Industry
Developed in collaboration with our raster and vector OEM customers, as well as partners and members of the Dyndrite Developer Council (DDC), the new Toolpathing API toolsets open new opportunities for both software and hardware development for the AM industry.
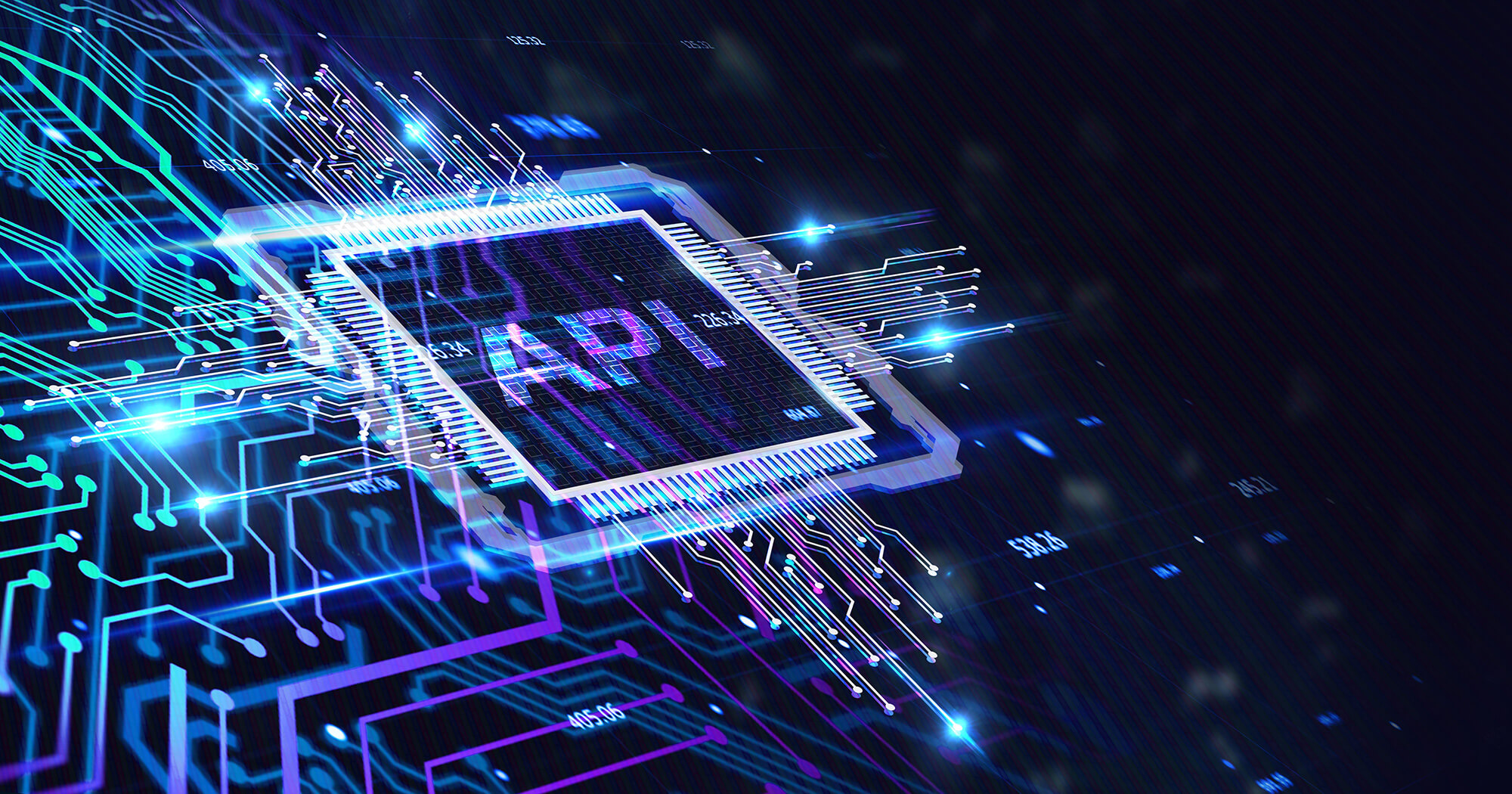
On April 20, 2021, at the annual Dyndrite Developer Conference, Dyndrite CEO, Harshil Goel, revealed new tools within the Dyndrite Accelerated Computation Engine (ACE) Toolpathing API. Developed in collaboration with our raster and vector OEM customers, as well as partners and members of the Dyndrite Developer Council (DDC), the new toolsets open new opportunities for both software and hardware development for the AM industry.
Why is Dyndrite developing APIs?
Before discussing the APIs, I want to briefly explain what the Dyndrite ACE does, and why the Engine is important for both existing and emerging technologies. Before geometry kernels were developed, CAD systems were built from the ground up. They were proprietary and expensive, with inconsistent performance, features, and functions, and negligible interoperability. These CAD workstations, including those from Intergraph, IBM and Computervision, cost hundreds of thousands of dollars. The barriers to entry into the CAD market were very high. The subsequent rise of geometry kernels in the mid 1980s, most notably ACIS and Parasolid, changed this paradigm. These new development stacks delivered a set of 3D tools that anyone could license and use to build design or manufacturing software. These kernels significantly lowered the cost of entry into the 3D CAD/CAM market, resulting in highly affordable 3D CAD/CAM applications running on much cheaper PCs, which were already being adopted by a worldwide engineering audience. In summary: These kernels democratized 3D CAD/CAM by delivering the fundamental mathematical tools that enabled new product innovation by a larger, more diverse customer base.
Fast forward 40 years to the additive manufacturing market today. Most additive software is still written using these original kernels. These kernels are not tuned to the unique mathematical geometry and compute challenges of additive manufacturing machines and processes that are emerging today: Voxel processing with metadata and grayscales, use of distance fields (and others) for geometry interrogation and segmentation, lattices, fine support structures, and more. While some of the larger additive machine OEMs have chosen to fill the gaps with internal software departments, they carry a high cost of development, and are limited by the legacy kernels of the 1980s.
What does this mean for smaller OEM start-ups and companies who have novel machines and processes, but lack math and software expertise to figure out the advanced algorithms they need?
Just like the development of the geometry kernels in the 80s, Dyndrite offers a modern, higher level of abstraction that empowers the hardware and process development community in solving the digital-to-physical transformation. It was created by mathematicians, computational scientists, and mechanical engineers to empower the pioneers seeking to bring innovative machines and processes to production environments. It provides powerful, yet accessible interfaces, so hardware champions can develop quickly with a committed software partner. It enables OEMs to drive their own unique raster or vector process without the need to hire large software teams, or the need to communicate intricate, often proprietary details of the process to the software partner. Dyndrite is lowering the costs and barriers to bringing a new process to market, while enabling new technologies with a more capable and flexible toolset. We are democratizing the critical compute software layer needed for continued innovation in additive manufacturing.
This is a step change for software in the AM industry. We are providing a math department so everyone can benefit from the emergence of new solutions.
Toolpathing API
Dyndrite’s Toolpathing API was designed for both raster and vector machine processes. Our recent developments have concentrated on some of the newest and more complex challenges faced by modern voxel and pixel-based AM processes, as well as a highly desired capability for vector-based metal machines.
These are:
- Control over RGBA and distance fields for functional grading in raster processes to increase repeatability, quality, and new multi-material processes
- Anisotropic compensation in raster processes to improve part dimensional accuracy and rapid calibration of new materials and processes
- Support-free metal additive through field-based segmentation to improve feature resolution, and reduce post-processing complexity
Color Channels (RGBA) and Distance Fields
In a production environment, additive manufacturing must adhere to tight tolerances, be predictable, and repeatable. This needs to persist as the machine size and resolution continues to increase, requiring an ever increasing amount of information to be processed.
The RGBA feature set enables the calculation of grayscales in voxels to determine:
- Key Part Segmentation, such as: core, shell, lattice structure, supports, inside volume, and outside volume, etc.
- Creation of useful metadata to refine the fundamental physical machine process, e.g. controlling ink bleed or light scattering.
- Definition and voxel level control of functionally-graded materials
The use of grayscale helps deliver new ways to address the development of fundamentally new physical processes. The APIs enable the programmatic generation of images to multiple color planes to enable manufacturing of challenging multi-material part families including induction coils, heat exchangers, wear pads and indicators, graded RF or nuclear materials, etc. This extra dimension, now available in the Toolpath API, will enable the additive manufacturing of these classes of parts while improving control for surface finish and feature resolution of most processes.
Anisotropic Compensation
Anisotropic compensation enables additive toolpath adjustments that account for the direction of print, the direction of recoating, and the direction of the deposition/fusing tool travel. Different axes often benefit from different scaling or offsetting to enable fine feature resolution. For AM to achieve mainstream manufacturing adoption, we need tight tolerances with flexibility and repeatability, and we must develop these toolpaths faster than the machines can execute them. Today we spend hours, sometimes days, compensating for a machine and material process, in the hope that the final part will meet requirements. There need to be faster tools to help solve these issues.
We have built additional compensations into the Toolpathing API to do just that. By giving the engine six scalar values - three for scaling in X, Y, and Z, and three for offsetting along the same axes - you can now address these process compensation challenges with a higher likelihood of success.
This means end users can more quickly develop new machines to process new materials, and also expand existing processes to new part families, while enabling more rapid qualification through improved repeatability.
This toolset is currently focused on binder jet and photo-polymer processes, although it is being expanded to other additive technologies.
Support-free Metal Additive and and Distance Fields
Arguably the hottest topic of metal additive since early 2020, the ability to produce a broader range of support-free parts was first heavily promoted by Velo3D. This was soon followed by EOS, SLM Solutions, and most recently, 3D Systems. Support-free metal additive reduces material usage for existing part classes, and enables new ones by reducing the downstream processing complexity of removing support structures.
While machine builders' approaches vary, much of the ability to print support-free relies on the generation of laser toolpath/parameter strategies appropriate for part geometry. This is achieved by altering the settings for different regions of the part, rather than relying on a few basic parameters commonly available in earlier machines. Achieving support-free metal additive is largely about the basic algorithms, rigorous bookkeeping, and compute efficiency.
To enable support-free parameters, our API works to segment the part at resolutions finer than the minimum feature size and allows programmatic assignment of unique parameters to different volumes within a part. This provides the tools to minimize distortion and ensure high part quality while reducing downstream processing. Our GPU architecture scales to deliver results at speed, for even the most complex of geometries. OEMs can develop their process on ACE to retain their process-specific competitive edge.
High Complexity, Resolution, and Control
In addition to focused toolsets and a new, modern geometry engine, Dyndrite is built on top of GPU acceleration and Python-driven automation tools. The GPU acceleration is designed to allow software to catch up to the capabilities of modern additive hardware. With significantly faster slicing and voxelization you can simulate and test more quickly to produce more complex parts, certify these parts and materials more rapidly, and increase production rates through robust automation. Our goal is to enable additive manufacturing to realize its advertised potential.
As machine and process innovators, the last thing you want is to be limited by the software tools around you. The Dyndrite Engine, it’s growing list of APIs, and partner applications, such as HP’s Universal Build Manager, provide a rich and rapidly expanding ecosystem to tap into.
Find out more at: dyndrite.com.
Find out more on this topic by attending Dyndrite Developer Conference 2021, April 20-21 (virtual event)
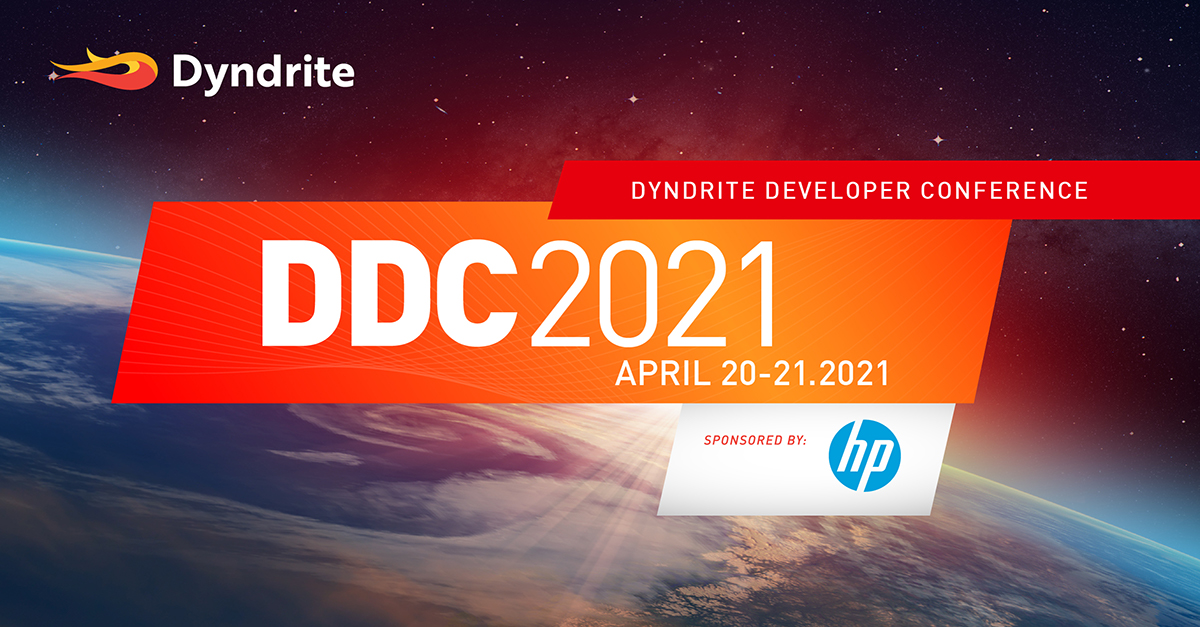