Why Dyndrite LPBF Pro, Why Now?
LPBF users are moving beyond prototypes to full-scale production, and the “good-enough” tools of the prototyping era no longer cut it. Today’s additive manufacturers need advanced software to accelerate materials development, part qualification, and high-volume output—capabilities legacy software can’t deliver. Discover why Dyndrite LPBF Pro is the right solution—and why the industry needs it now.
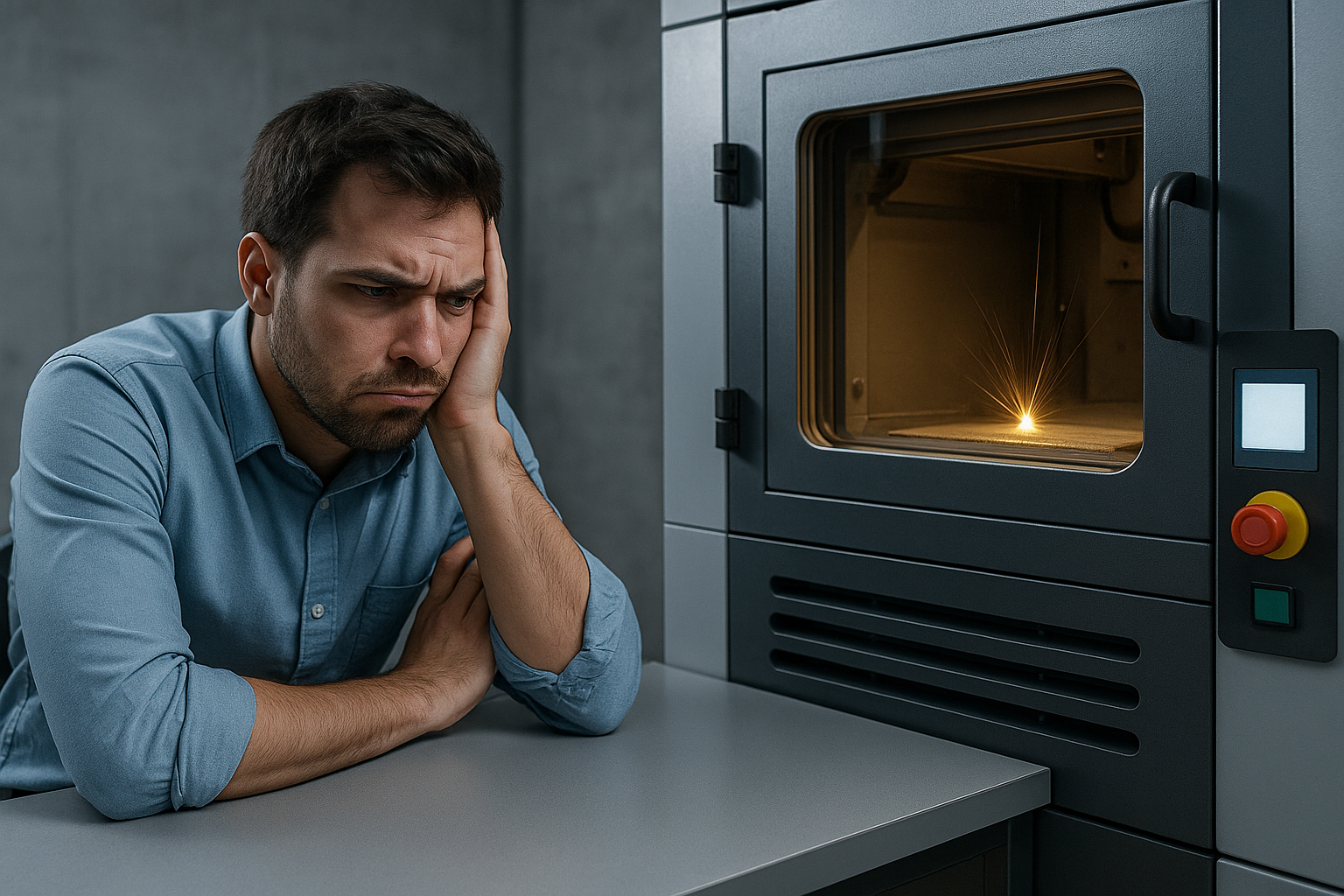
For decades, additive manufacturing (AM) has been stuck in a cycle of incremental improvements—tweaking outdated software, wrestling with rigid qualification processes, and struggling with tools never designed for true industrial-scale production. The result? Bottlenecks, inefficiencies, and an industry struggling to bridge the gap between promise and reality. It’s time for a new approach. We’re done waiting.
Additive manufacturing, especially Laser Powder Bed Fusion (LPBF), has experienced tremendous growth, revolutionizing highly regulated industries like aerospace, defense and propulsion. Yet despite these advancements, LPBF usage remains limited, rigid and lacks creativity. At the heart of these limitations lies one glaring issue: a distinct lack of control.
The Control Problem in Metal LPBF
LPBF, like other AM processes, depend heavily on slicing software to generate toolpaths. Legacy slicers, some developed for rapid-prototyping, often leaves engineers and technicians working blindly within rigid constraints – significantly hindering productivity, innovation, and material exploration.
At Dyndrite, we fundamentally believe control must reside where it belongs—in the hands of the engineers and operators who understand their machines, materials, processes, and end applications intimately. Why rely on arbitrary settings dictated by software built without modern, industrial-scale manufacturing in mind?
One Parameter Does NOT Fit All
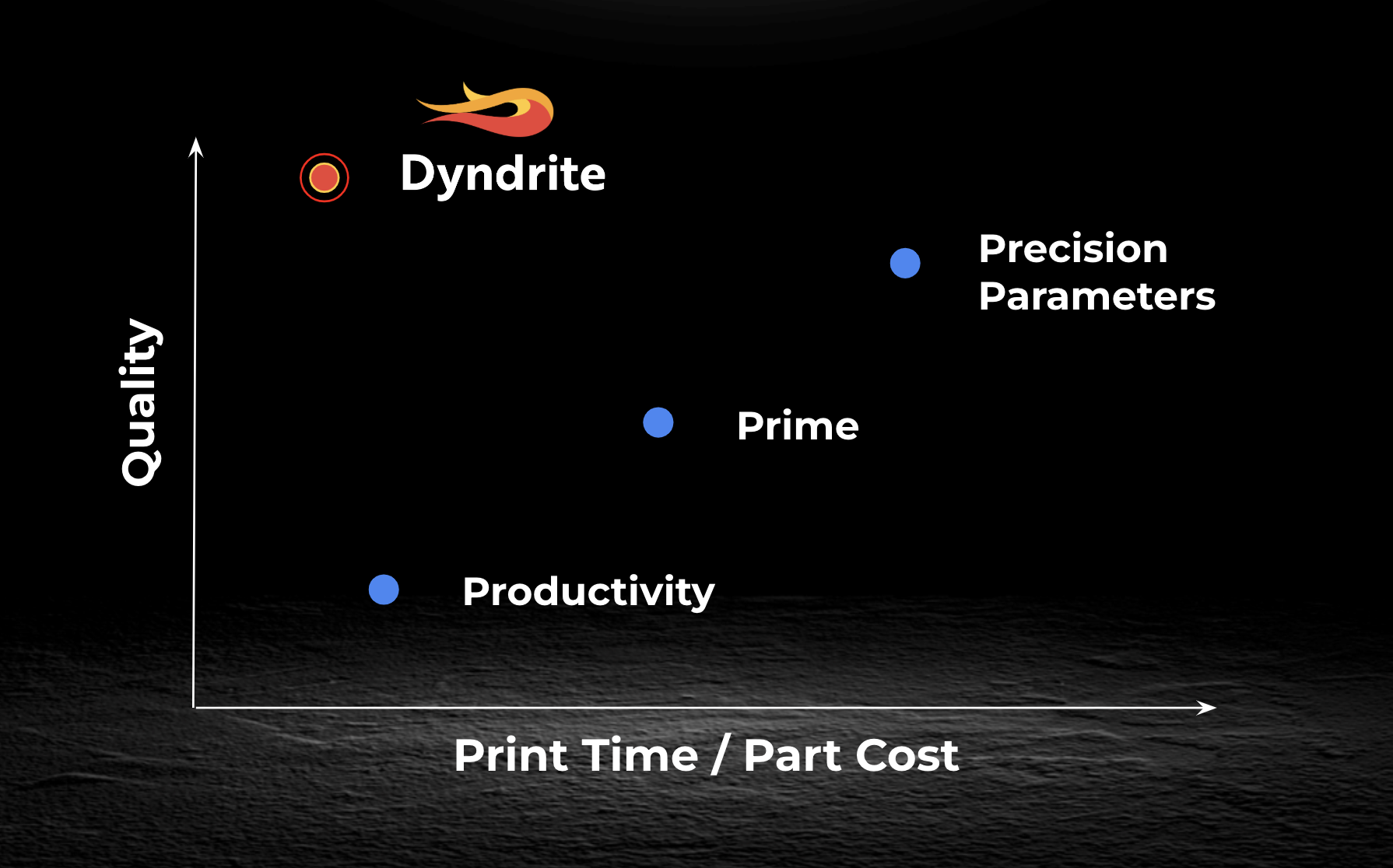
One glaring example is parameter development and assignment — the fundamental nature of which is flawed. Legacy AM applications limit the assignment of one parameter to one part. Users then acquire or painstakingly develop "good enough" parameter sets based on whether they want to go fast, print precisely, or somewhere in the middle. Dyndrite does away with this limitation. Users can now assign multiple parameters within a single geometry — developing specific parameters for specific features or characteristics of the part.
Consider two seemingly simple geometries: a solid metal cube measuring 1cm3 and a lattice structure cube of identical dimensions. If we naively use the same laser parameters optimized for one geometry to print the other, the deficiencies become immediately clear.
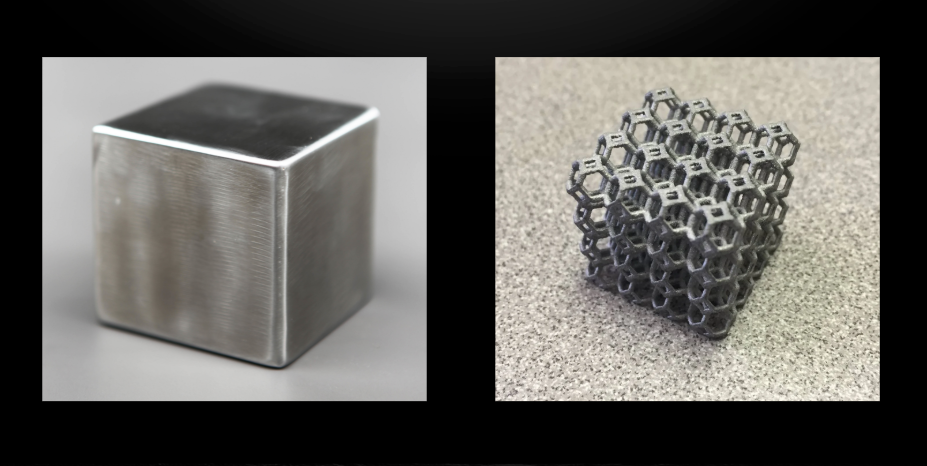
Printing the solid cube with parameters suitable for the delicate lattice will result in excruciatingly slow build times, drastically reducing machine throughput and production efficiency. Conversely, printing the intricate lattice cube with parameters meant for the solid cube would create catastrophic melting, resulting in a molten blob.
Why, then, does the industry continue to accept this inefficient approach as standard practice?
Look at CNC machining—a mature, productivity-driven industry. Any respectable machinist would never use the same speeds and feeds for roughing operations as they would for delicate finishing passes. The industry understands clearly that different operations demand distinct, optimized parameters. Why, in additive manufacturing, do we accept any less?
Good Manufacturing Software Demands Precision Control
Good manufacturing software isn't merely about generating “one size fits all” parameters—it's about intelligent, informed decision-making and telling the machine exactly where to do what, when. It's about empowering operators and engineers with the flexibility and control to optimize their production based on the geometry, the material, and the specific end-use application requirements.
Dyndrite LPBF Pro delivers precise control without compromise. It shifts the paradigm from assigning generic parameters, to geometry-driven intelligence, allowing users to apply different laser parameters within the same build, based purely on the specific requirements of each geometry. With this approach, users achieve unprecedented optimization in material usage, print speed, and overall part quality.
Dyndrite LPBF Pro allows users greater flexibility, increased throughput, reduced cost-per-part, and improved part quality and smoother surface finish.
Why Now? The Manufacturing Shift is Here
Industries relying on AM and LPBF are rapidly shifting from prototyping to serial production, and legacy software tools simply cannot meet these new demands. Today's competitive landscape requires flexibility, precision, and automation to remain viable. Companies clinging to outdated tools risk falling behind as competitors leverage smarter, more advanced techniques and software solutions.
Dyndrite LPBF Pro: The Future of Additive Manufacturing Software
So, while Dyndrite LPBF Pro slices files, it is not just another slicing software, it's high performance manufacturing software purpose-built for the modern era of additive manufacturing. With GPU acceleration, scriptable automation, and advanced multi-parameter toolpathing, it empowers AM users to optimize manufacturing processes precisely and effortlessly.
In the race toward industrial-scale additive manufacturing, control is everything. With Dyndrite LPBF Pro, that control is back where it belongs—in your hands.
Ready to take back control?
Talk to a Dyndrite LPBF Pro expert today and discover how to maximize your additive manufacturing capabilities.
Interested in touching Dyndrite LPBF Pro with your own hands? Signup to attend one of our local, hands-on workshops being held in key manufacturing hubs worldwide. Here LPBF professionals like yourself will learn how to unlock groundbreaking part printing capabilities, boost workflow, machine productivity, and achieve repeatable, high-quality 3D metal printing results. Click here to Find a Roadshow Near You
Find out more on this topic by attending Dyndrite Developer Conference 2021, April 20-21 (virtual event)
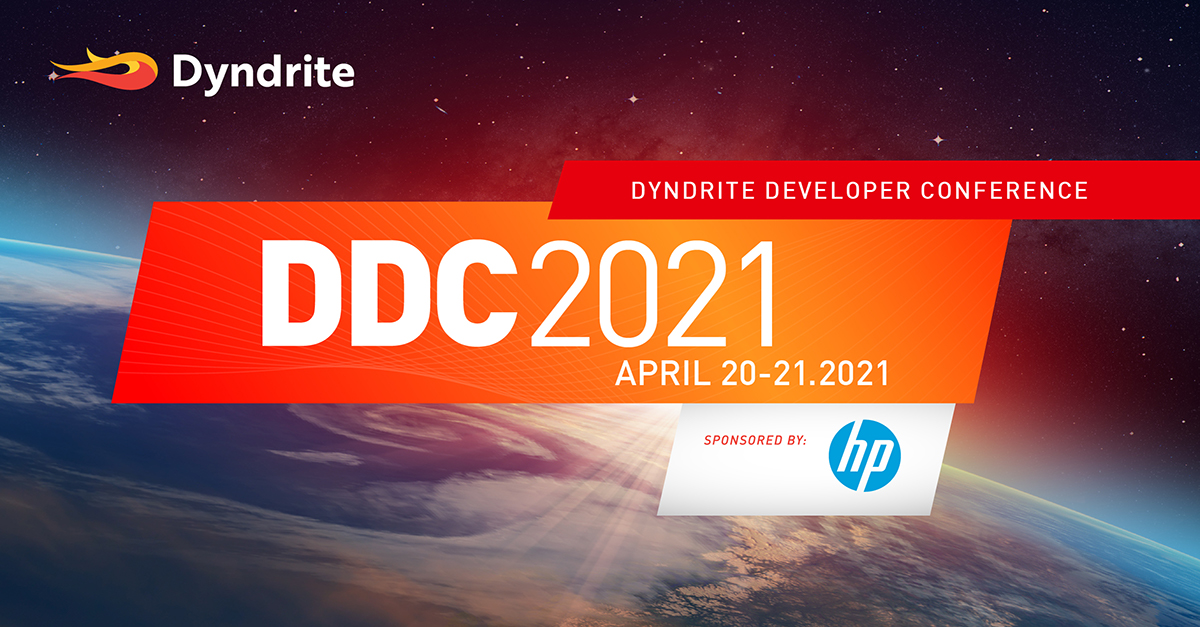