Change Has to Start at the Software Level
Episode 2. The second article in a 5 episode series by Stephen Anderson, VP of Business Development, Dyndrite
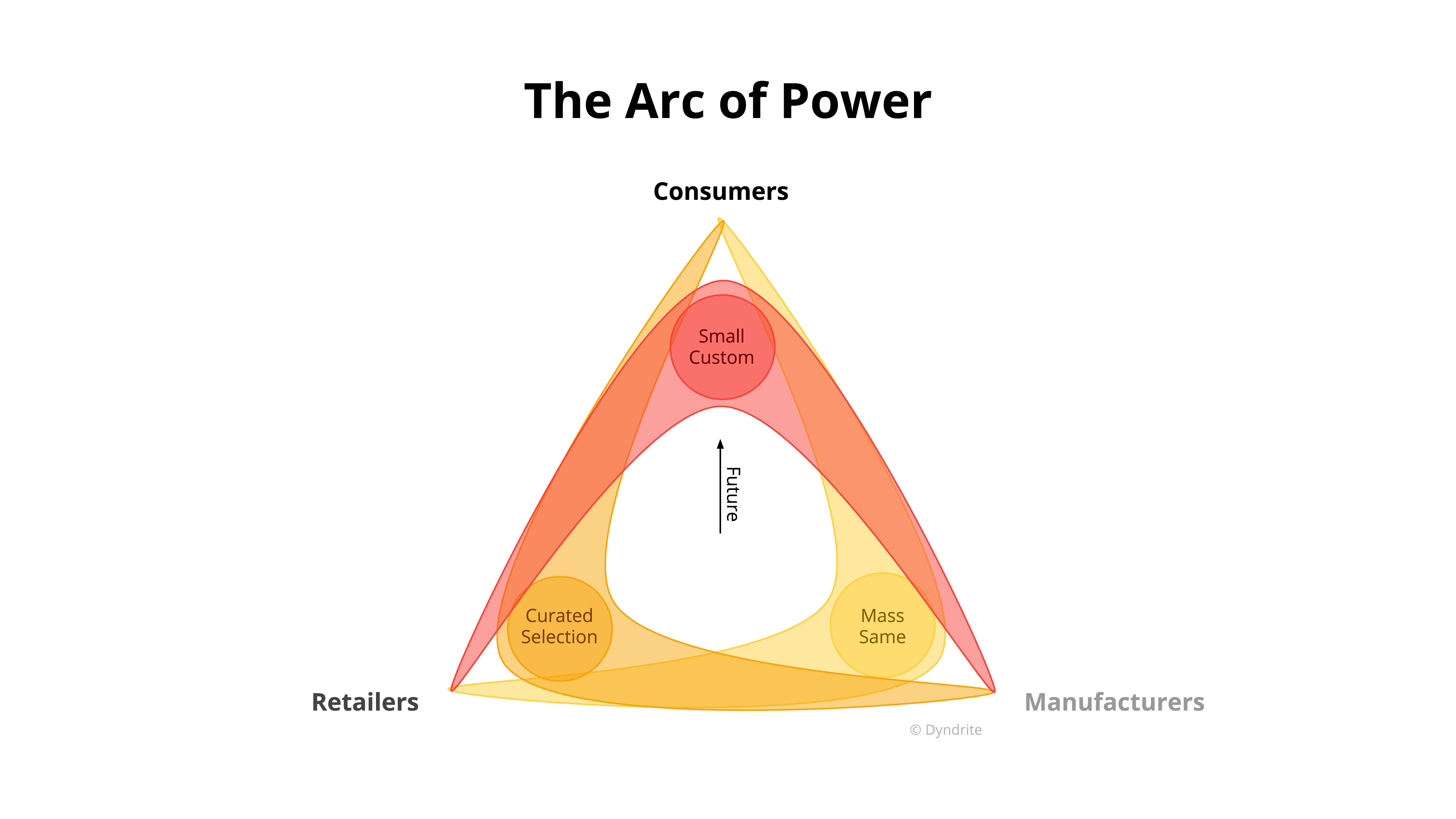
It is generally accepted that manufacturing has to change in the wake of the COVID-19 epidemic. Reliance on off-shore centralised manufacturing models needs rethinking, supply chains need to be radically shortened, on-shoring and local manufacturing is back in fashion and manufacturers need to implement flexible production. With such a concentration on agility it is recognised that manufacturers need to implement digital transformation in their factories, upskill their workers and introduce new make methods such as Additive Manufacturing. And that they need to do this NOW!
On June 30 2020 I attended the Dyndrite Digital Manufacturing Investor Day (DMID) which remotely brought together almost 200 attendees and crucially more than 80 investment firms from Silicon Valley and worldwide. All were looking to hear about new manufacturing methods, technologies and start-up businesses that they can invest in.
Before the pitches a panel of experts moderated by Harshil Goel (CEO, Dyndrite) discussed the effects of COVID-19 on manufacturing and how such a global crisis is likely to bring about manufacturing change.
With a rally call of “Never let a crisis go to waste” Hap Klopp (Founder, The North Face) made several very interesting observations about how major change events deliver the stimulus and catalyst to radically disrupt societal, and therefore, manufacturing status quos. In other words, the old engineering adage of “if it ‘aint broke don’t fix it” often inclines manufacturers in periods of stability to not be disruptive and only look at incremental improvements. It takes a global event such as COVID-19, or the last Great Recession, to make us realise our manufacturing systems might need serious attention!
Hap also discussed how the power balance has changed over the last ~100 years, first from the manufacturer, then to the retailer and now to the consumer (see top graphic). He argued with the rising predominance of online consumerism – customers’ expectations are radically moving manufacturers to small volume manufacturing runs of ever more customised products that are required NOW!
This is changing business models, supply systems, and networks, and causing manufacturers to think more about how they can build products and supply chains with ever more flexibility. One such example is Voxel8 which is revolutionizing the printing of patterns on sports shoe uppers by directly printing them using elastomeric polymers combined with inkjet technology to create structural components, complex patterns and relief features. Coupled with a customer demand for sustainability (climate change), reduction in scrap rates and continuous improvements in product quality, now is the time to be implementing (re)configurable manufacturing systems: Using Industry 4.0 processes and technologies such as additive manufacturing, automation and robotics that can be repurposed easily for changing product demand.
The COVID crisis helped additive manufacturing gain recognition for its ability to rapidly pivot to producing PPE devices, while traditional manufacturing has much less agility. But it also helped expose that additive is still not widely regarded as a truly viable production solution. Why is that? We believe it is due to the limitations that remain because of the current, antiquated software offerings available for design, manufacturing, monitoring, analysis, robotics and more. We’ve been using the same software for over 30 years, and most haven't kept pace with advances in design thinking, new computing paradigms, or manufacturing advances - we are literally at a point where the manufacturing hardware, especially in additive, has surpassed the software. It’s time for a change.
The industry needs a new foundation upon which to build a modern digital manufacturing ecosystem upon. One designed to use every bit, register, and clock-cycle available, one that inherently scales based on your ROI needs, dramatically increasing productivity the more you use it, and most importantly, a new digital nervous system that unleashes human creativity. That is the change that Dyndrite brings.
Find out more on this topic by attending Dyndrite Developer Conference 2021, April 20-21 (virtual event)
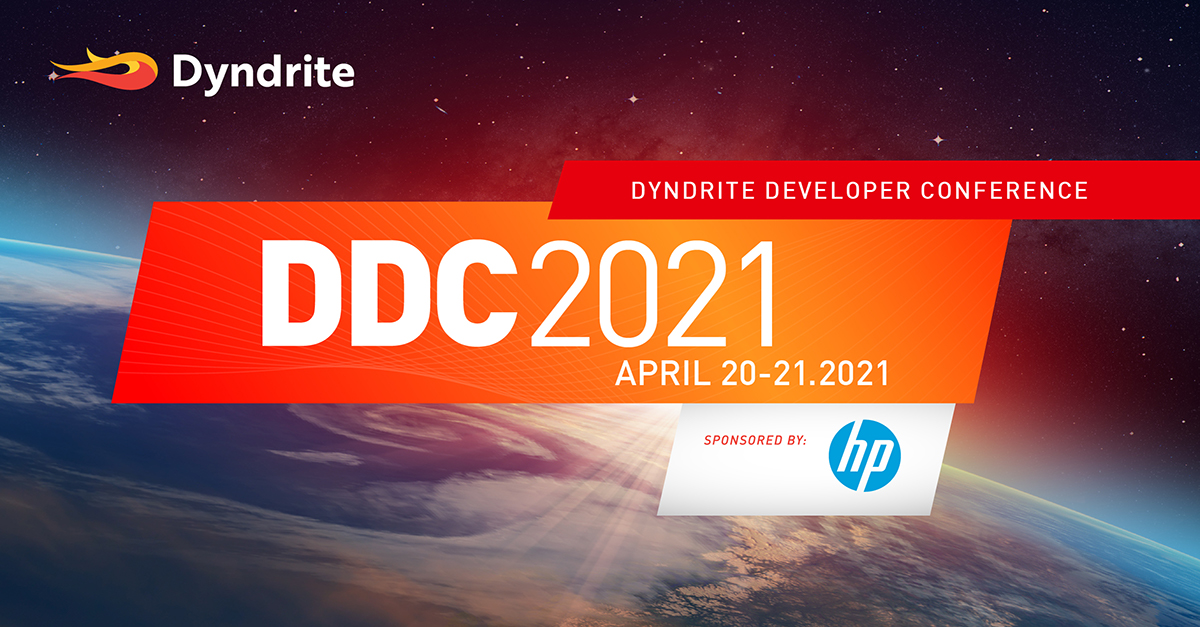
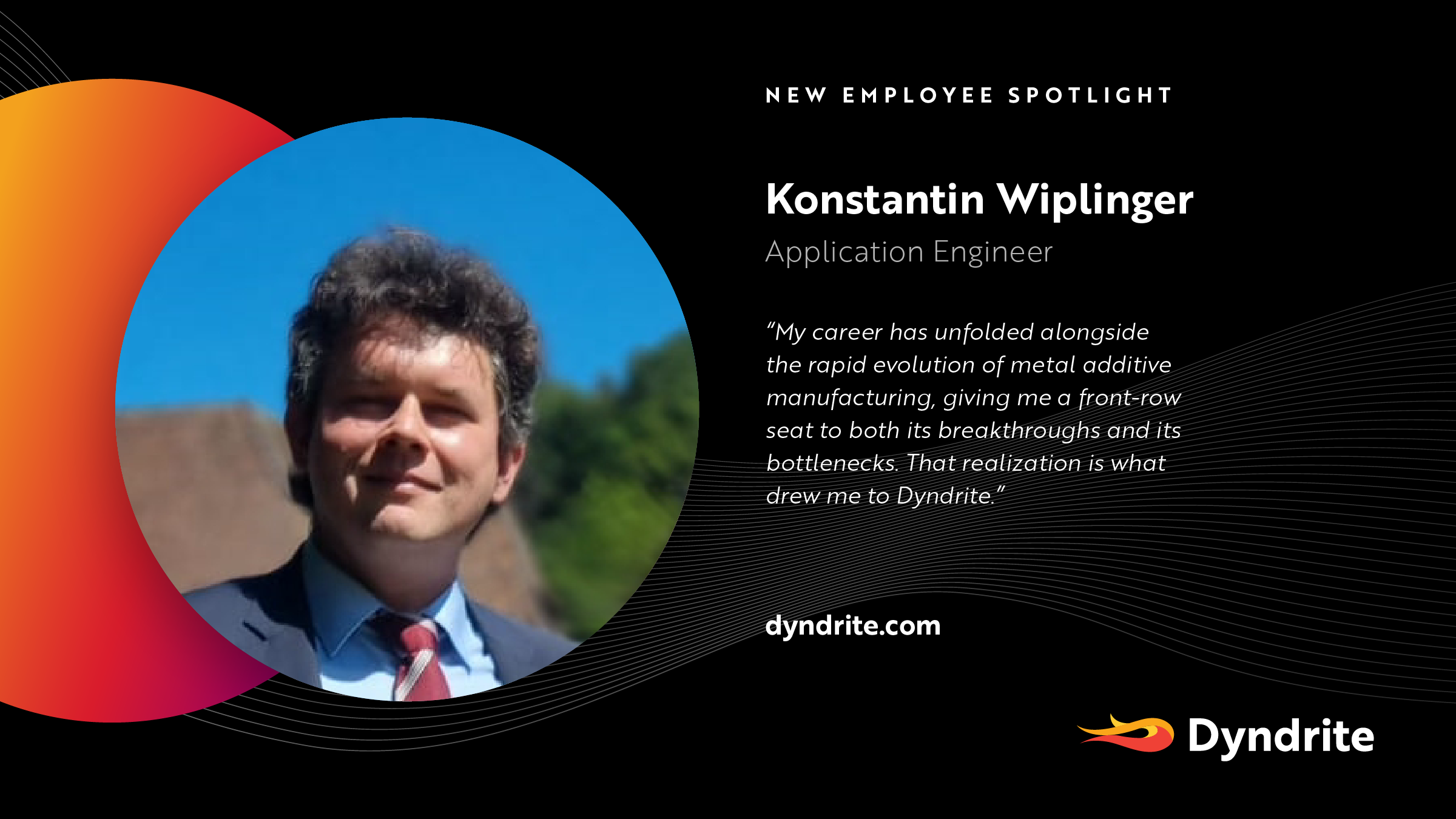
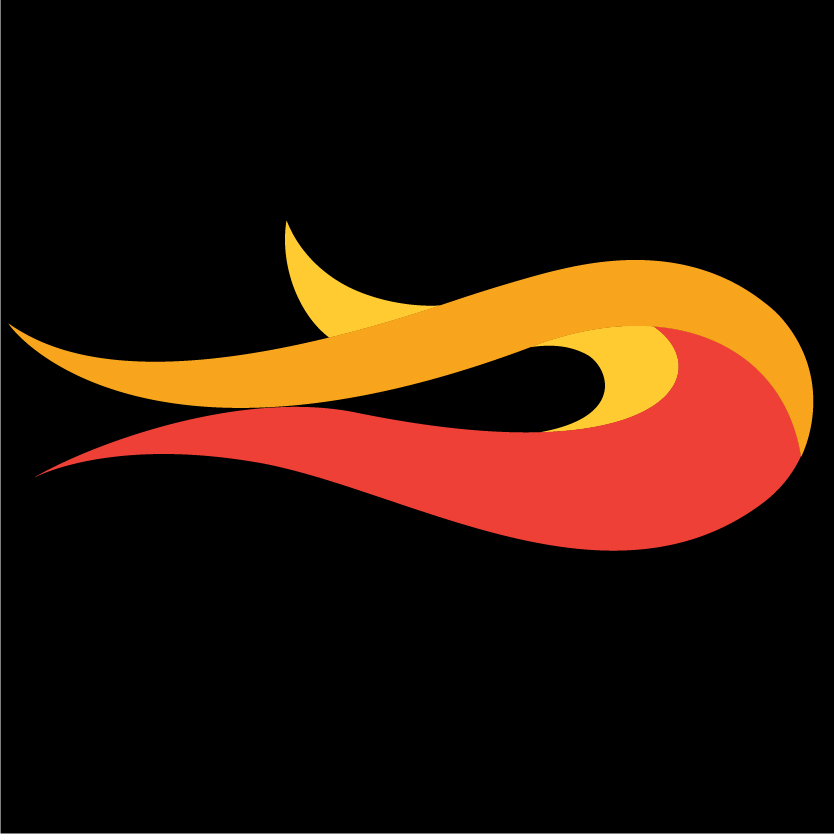
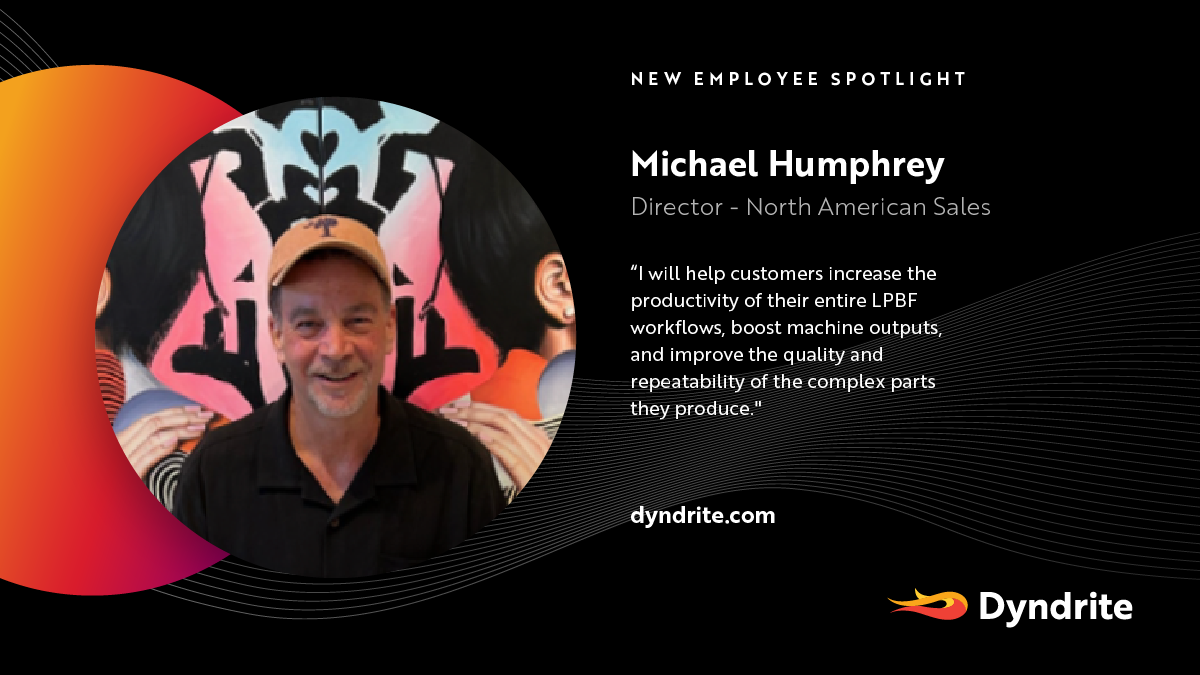
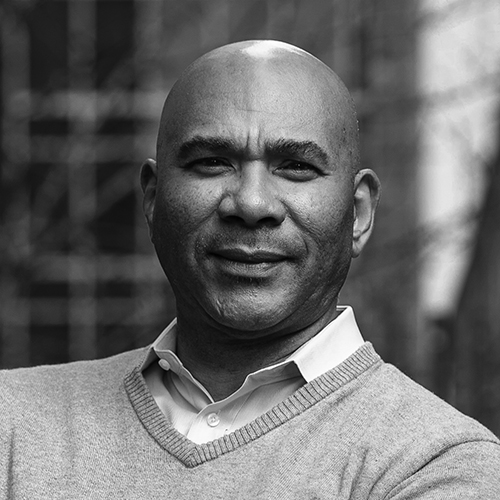