AGILE, DIGITAL, ADDITIVE MANUFACTURING?
Episode 3. The third article in a 5 episode series by Stephen Anderson, VP of Business Development, Dyndrite
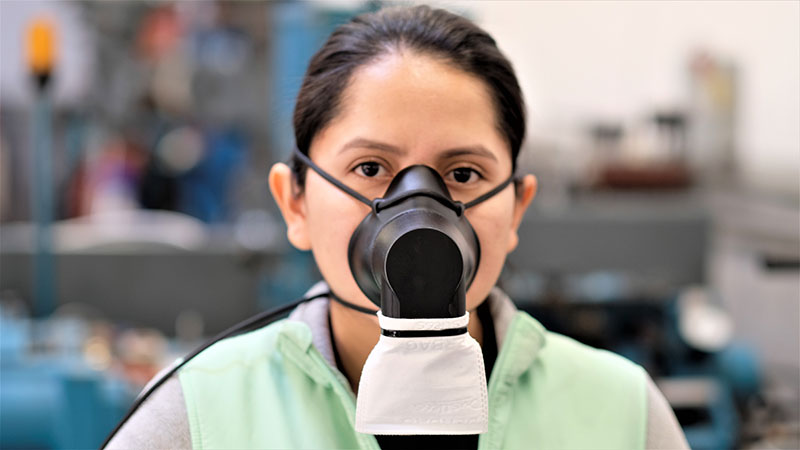
Image: Additive’s COVID-19 response, Photocentric worked with Long Island Racing to manufacture M1 respirator masks for first responders.
Agile, Digital, Additive Manufacturing - these three sentiments are echoing everywhere in the manufacturing press. Additive manufacturing proved itself during COVID. But can we continue to press the advantage and prevent manufacturing from simply going back to the status-quo? Similarly, how “Agile” or “Digital” is additive manufacturing really? And if it’s not, what’s holding it back?
To start, here’s some recent examples of AM in the press:
June 11 - Manufacturing requires radical rethink in post-Covid era
“A recent survey of German manufacturers and students by Pinsent Masons revealed the following: “…disruptive technologies … are changing production processes, sparking a fresh industrial revolution - commonly referred to as Industry 4.0…the strategic priorities for German industrial businesses included improving use of technology … and a next wave of digitization.
76% of students said it was either ‘very important’ or ‘indispensable’ that the organisation they join be at the cutting edge of new technology.
Climate change was also likely to have an impact on business, with 38% of companies saying it would have a significant impact on production.
50% of respondents either had, or were planning to, make significant changes to internal training. Meanwhile, 23% had made changes to their agile working environment, and a further 23% had planned to make changes to agile working.” https://www.pinsentmasons.com/out-law/news/manufacturing-radical-rethink-post-covid-era
June 29 - Responding Resetting and Reinventing UK Manufacturing Post Covid-19
“Looking forward the report analyzes the opportunities for building a new economy with a renewed manufacturing sector at its heart. In particular ... the need for digital skills that can support the adoption of technology .... According to Make UK this will require the skills to support a digital transformation which must now be a national strategic priority with the creation of a National Skills Task Force.” https://www.makeuk.org/insights/reports/responding-resetting-and-reinventing-uk-manufacturing-post-covid19
And also take a look at this blog from Dassault, “For AM, and particularly plastic AM, COVID-19 presented an opportunity to show what it could do. With major medical supply manufacturers shut down, or unable to ramp up production of PPE quickly to meet demand; multiple organizations: universities, research institutions, prototyping departments, 3D print manufacturers and even individuals with their own home printers, stepped in to produce plastic face masks and other plastics components. This often-localized production successfully plugged the supply/demand gap and got PPE into hospitals, first responders and other frontline personnel. Similarly, 3D print manufacturers of products such as glasses frames easily switched to making custom protective eyewear and still others moved from making custom footwear to Powered Air-Purifying Respirator (PAPR) hoods and associated respirator components.” https://blogs.3ds.com/northamerica/additive-manufacturing-in-the-covid-19-spotlight/
One stellar example of the power of 3D printing of PPE has been demonstrated by Photocentric, a recent member of Dyndrite’s Developer Council, who recently won a UK Government contract to produce 7.7 million face shields for the NHS.
To fulfil the NHS contract Photocentric designed and installed a purpose-built factory to house a print-farm of 45 of their Magna printers. The Liquid Crystal Magna is a large LCD printer with a 510 x 280 x 350mm build volume that can create either very large objects or multiples of small parts.
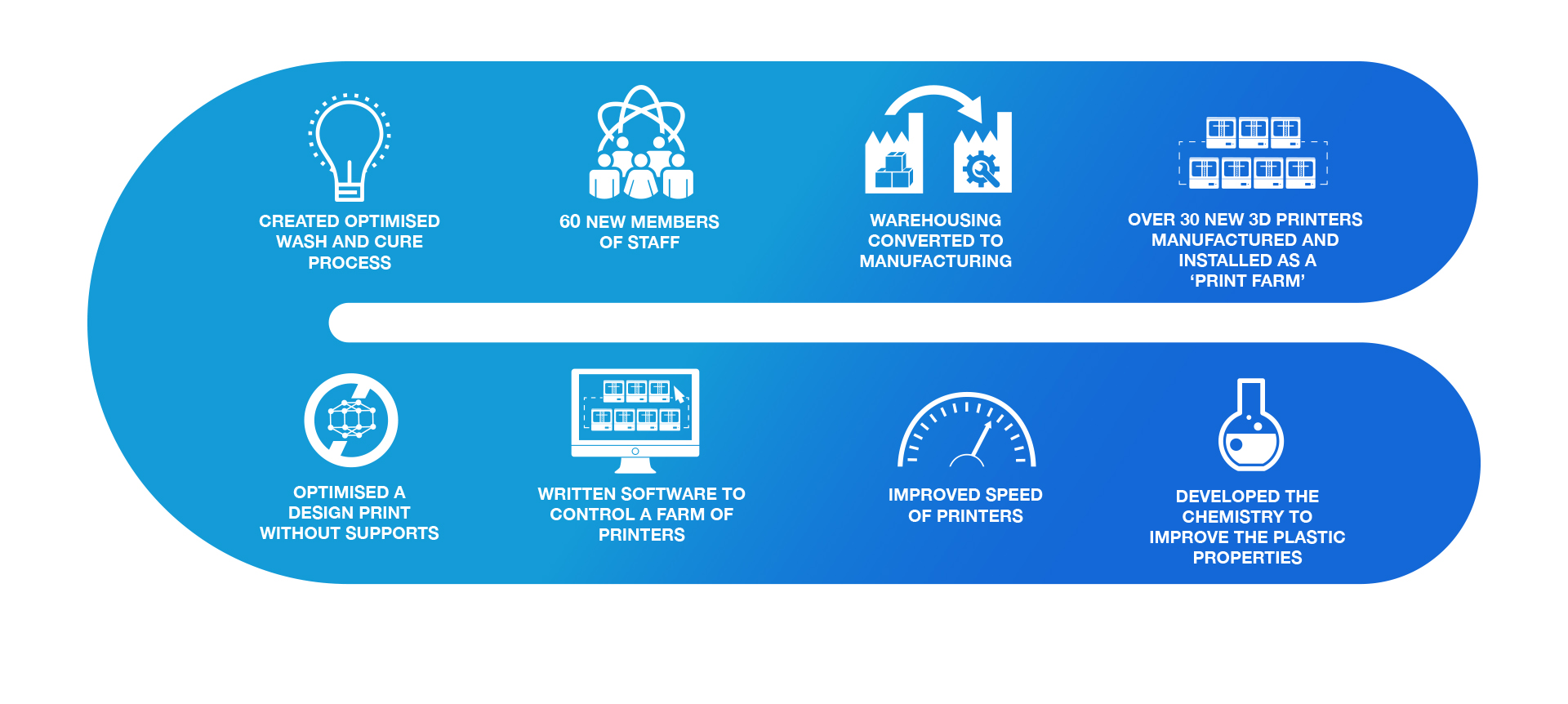
Photo credit: Photocentric, The changes needed to develop the Magna Print farm
To achieve the production scale required Photocentric had to create a print-farm, develop the process, hire and train new staff, write new production management software and further develop resin chemistry, all in a few weeks.
Operating 24/7, Photocentric is making over 50,000 3D printed components every day and is scaling the farm up to create over 500,000 items a week. With over 2.3 million parts already made Photocentric has truly shown how 3D printing flexibility can scale quickly.
To see more on the fantastic story behind Photocentric’s NHS contract, see https://youtu.be/VQvHAgvk19w
Of course, it can be argued that these efforts are making simple, albeit vital, products that do not require much in the way of QA certification or FDA approval. Even so AM has demonstrated the power of instantly being able to retool, make something else, make it locally, and make it fast.
With collaborative communities springing up and able to share files digitally the success of AGILE, DIGITAL, ADDITIVE MANUFACTURING in plastics has been proven. What remains now is to build upon these lessons for a more digital future.
Has COVID-19 Impacted Metal AM?
Without a doubt, yes and hard. Metal AM has not been directly involved in what is mostly plastic PPE production and the landscape for this technology is a little different. Since COVID, for AM metal production, AMPOWER reports a slowdown in demand from aviation, especially for the likes of Airbus and Boeing, with Boeing additionally battling its 737Max crisis. There is also a reported slump in demand for metal additive in oil and gas where the oil price has slumped due to less travel and less energy production for industry. However, for automotive their prediction is more optimistic, with metal AM playing a continued role in prototyping (and I would argue tooling). Similarly, for metal medical devices demand is likely to remain strong. AMPOWER notes the success of plastics during COVID-19 but for metal states:
“High part and qualification requirements, complex manufacturing and post processes as well as the need for lengthy certification through notified bodies limits similar reaction times for metal AM technologies. Metal AM is often caught in the middle of supply chains of conventional technologies in a rather conservative industrial environment. ”https://additive-manufacturing-report.com/analysis/corona-impact/
However, one bright note is the news that SLM Solutions increased revenue in the first half of 2020 by 90% over last year. The press release noted that “The Management Board stated that it expects a revenue increase of at least 20% compared to the previous year for the full year 2020.”
https://www.metal-am.com/slm-solutions-reports-90-revenue-growth-in-first-half-2020/
Interestingly AMPOWER also suggests that COVID-19 will cause consolidation in metal AM and particularly Laser Powder Bed Fusion (L-PBF) machines saying…
“…(COVID-19) helps accelerate the necessary consolidation to refocus on the real value proposition of metal Additive Manufacturing.”
This statement is telling! Clearly it is saying that the current field of machine vendors is too large. But more than that I think it is suggesting that the way the metal AM (LPBF) business has developed has become counter-productive to its continued adoption.
To date machine vendors have developed I.P. and know-how as a means to differentiate from other entrants. This is now becoming unhelpful. Unlike say, Machine Tools, where a CAM toolpath can usually produce the same component on different machine types; too often in AM a tool path (assuming it can be even be produced across competitor machines easily – itself no small feat) will too often produce qualitatively different parts from a metallurgical and geometric standpoint. This inconsistency in metallurgy, based on parameter and tool path differences inside vendors’ machines effectively ties end-users to specific machine types for specific components and applications, and prevents wider adoption. Couple this with lengthy certification processes through notifying bodies means that qualified components are often only built on one machine type, forever! So, while the machine is still producing an AM component (with value-add) the production method is no longer Agile.
To conclude Part 3; how can machine vendors deliver systems that will consistently and reliably reproduce parts even when produced across different vendor platforms? That would need the establishment of standards (being worked on slowly but surely) but in my view also grounded on software that enables that. The current availability of many ‘home grown’ additive software solutions means that consistency is impossible - varying standards, feature sizes, ‘closed’ systems and little process control for the end user prevents that kind of consistency.
This is one of the broad industry challenges that Dyndrite has set out to solve.
Find out more on this topic by attending Dyndrite Developer Conference 2021, April 20-21 (virtual event)
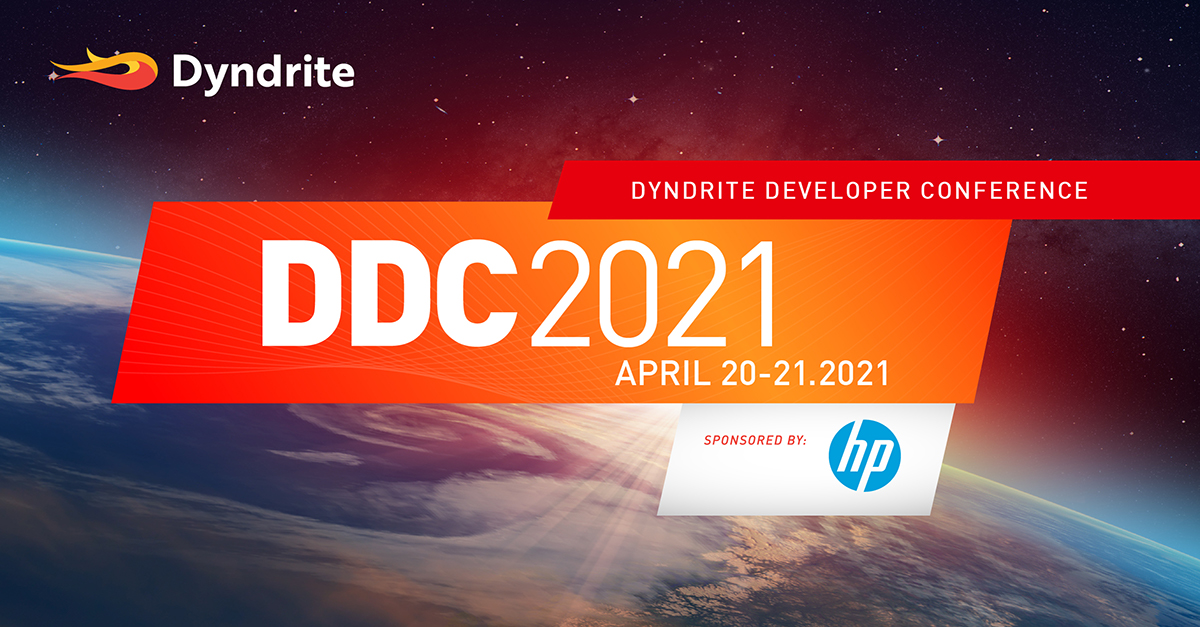
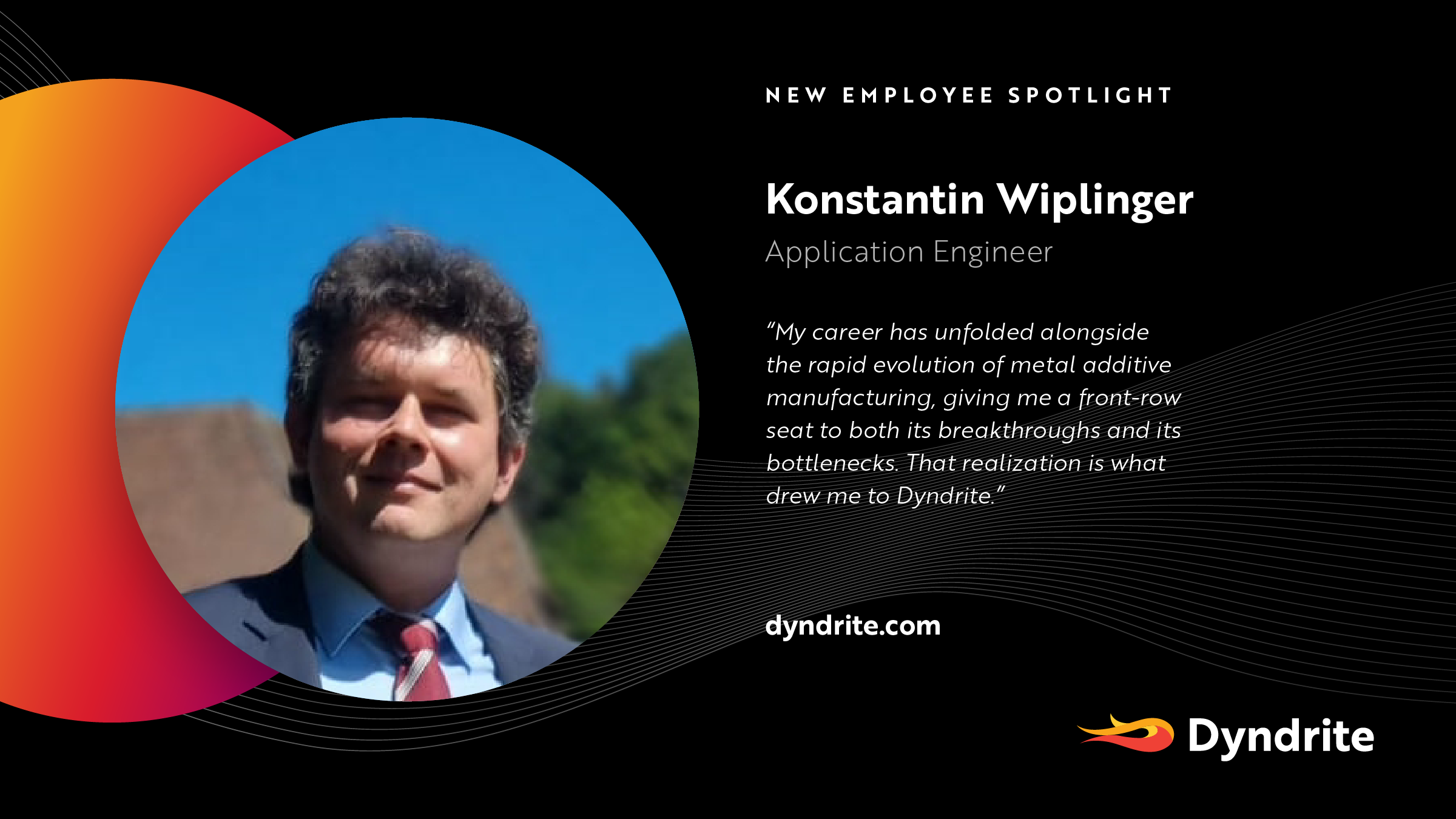
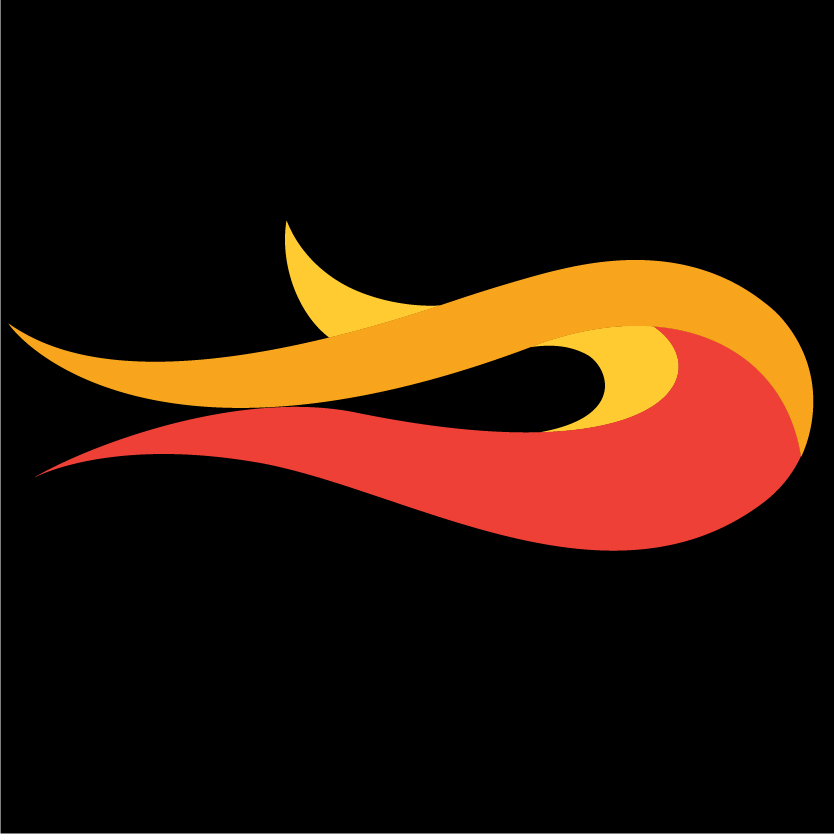
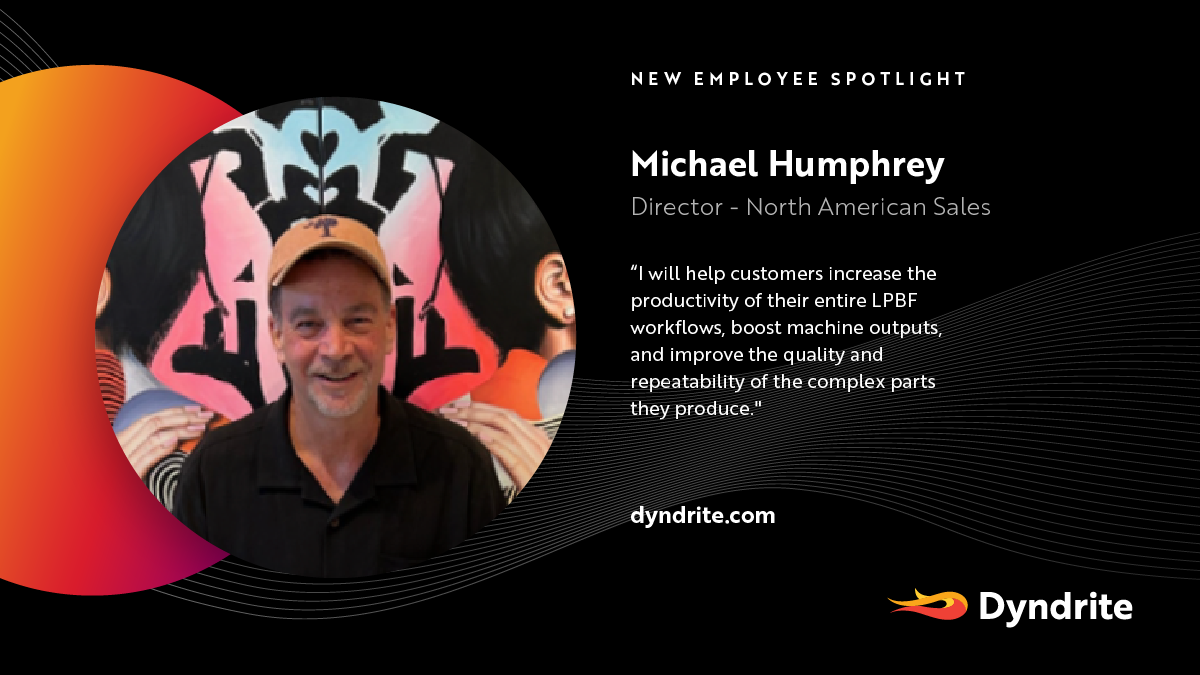
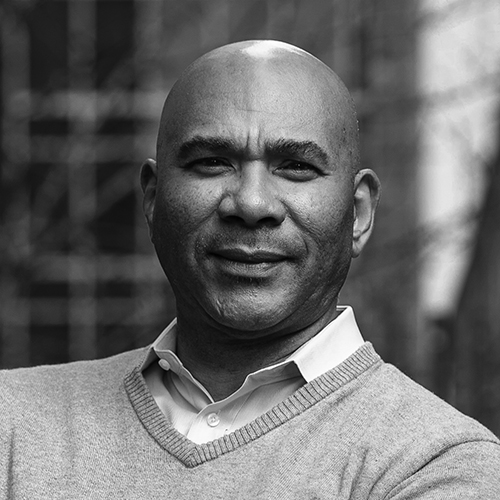