Why I Joined Dyndrite
Thoughts from Dyndrite’s newest employee on what Dyndrite means for the additive industries
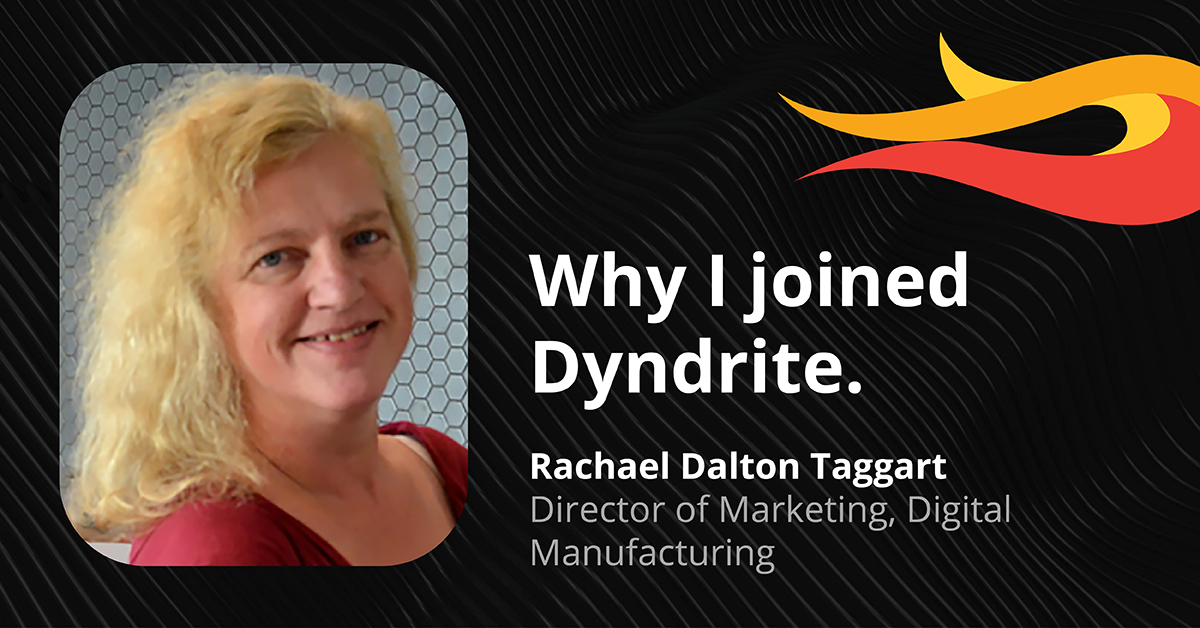
Almost a year ago I resigned from 3D Systems and became self employed as an additive manufacturing marketing consultant. It has been a year of some hard work but also an opportunity to read industry articles and papers, as well as a chance to contemplate my own professional future.
After 30 years in the 3D CAD, traditional and additive manufacturing industries, having time to read and think about it has been incredibly healthy and cathartic (I recommend it!) As a result of this I have come out with a number of conclusions about the industry -
- The additive industry is kind of like the Wild West right now. Hundreds of different hardware solutions in both plastics and metals, each vying against the competition with the adage of ‘better, faster, cheaper’ but typically lacking positive proof of the claims being made
- There are a growing number of point solutions that each claim to solve automation in additive when in reality they simply deal with one specific problem – without any true interconnection to other solutions
- There is an almost total lack of standards across the space – STL is the one true standard in place and quite honestly it shouldn’t be
Why does this all matter?
Well, they are all factors as to why I took a job with Dyndrite. Let’s take a closer look at the landscape.
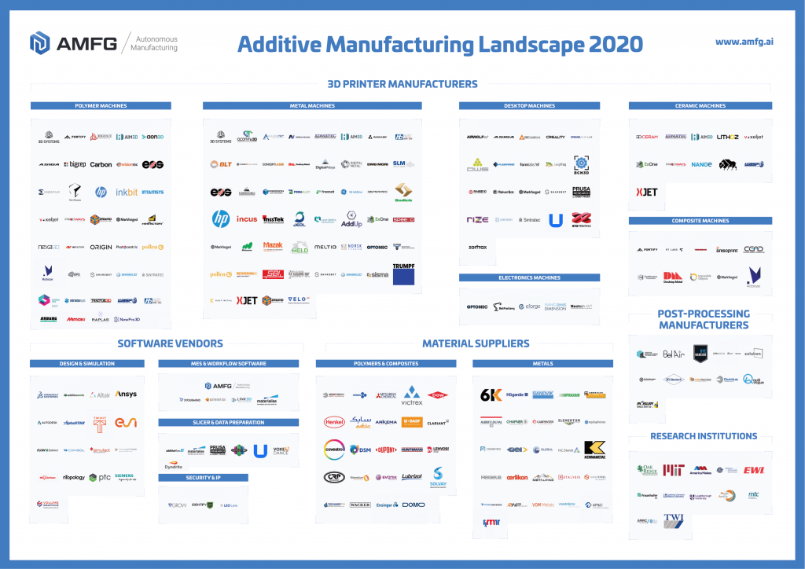
As can be seen from the chart there are now a multitude of new entrants across all types of Additive machines, in fact the vast majority of these companies have been founded in the last 10-12 years. They all offer unique machine features and/or lower cost options to differentiate from each other, and more importantly to stand out from the handful of traditional “household name” manufacturers who still dominate market share. This is particularly true of the explosion of new Far East manufacturers.
What this means is that competition is fierce, with many new players in the market and also customers now have an extremely broad, and confusing, choice of solutions. To make matters worse, most of these systems are closed and proprietary. The scarcity of open systems and standards is a problem for the entire industry. In traditional machining, you can run the same toolpathing data across different CNC machines and come out with pretty much the exact same parts, within tolerances. In metal additive, even if you could run toolpath data from one vendor’s system in another platform, the resulting parts would be quite different in quality, accuracy and feature resolution without a lot of time-consuming testing and adjustment of the process controls.
These factors are a barrier for the entire industry. As it stands for the industry as a whole to succeed, there has to be consolidation of the market – winners and losers – as well as open standards. I’ll get to the latter point in a moment.
Automation, or the lack thereof.
As part of my research in the last few months, I have been observing and tracking “automation” solutions for additive. There are lots of great ideas, new startups, lots of investment. But what struck me most about this segment is that most of these software solutions deal with just one aspect of the additive workflow, without any kind of interconnection with other software applications. Having said that, I think that Siemens’ automation tools for additive (and indeed the entire shop floor) is probably the most advanced solution available. But, as friends often point out to me, it is based on Siemens NX software and that is a barrier for many whose operations are exclusively on other CAD solutions.
Honorable mentions need to go to Link3D and AMFG, both companies working on comprehensive additive workflow process and monitoring solutions. In addition, on September 9, 2020, Authentise and Additive Guru announced a partnership to merge the companies’ process monitoring and workflow management solutions together - they see the light. But the rest of the solutions available mostly deal with a specific task – print build preparation, post processing, print monitoring, simulation and so on. What is clear is that very few, if any, of these solutions are able exist within a common ecosystem. That in turn means that customers have to cherry pick solutions and run them independently. This is inefficient and counter-productive!
It is clear that for the industry to be successful it needs software standards and open solutions that enable an easily integrated set of automation solutions that all interoperate and collaborate.
Standards are a necessity
As of now there is one standard within the industry and it is the STL format. Admittedly some stand-out vendors have started to offer direct CAD-to-print solutions for additive build prep but in the most part, STL remains. Given that STL is a 35 year-old format that creates an inaccurate approximation of the design, is difficult and bulky to handle, and has to be repaired all the time, you have to ask, why on earth is this still in use?
No offence to my old friend Chuck Hull, who was ultimately responsible for bringing STL to the market, but I think even he would agree that STL should have gone a long time ago. To build the industry into true production grade, STL really has to go in favor of the mathematically pure and computationally scalable 3D CAD data we should be using.
But what standards should we have? In the April 2020 Dyndrite Developer Council event, Harshil Goel CEO of Dyndrite stated, “We can’t possibly have 30, 40 or 100 separate printer companies all with different competing standards.”
As referenced earlier in this article, the lack of standards across the industry are damaging to both vendors and customers alike. Reduced productivity, a slowed momentum, lack of repeatability across disparate platforms. Something needs to change for the industry to succeed.
Dyndrite offers that possibility. As a ‘ground up’ development environment and kernel, Dyndrite offers a completely new way to build additive manufacturing software and hardware solutions - rapidly. Harshil Goel often cites the revolution that the combination of Adobe PostScript and the Motorola 68000 wrought on the 2D printing industry more than 3 decades ago. Dyndrite, with its GPU-based compute, native CAD-to-print workflows, and Python scripting API, has every opportunity to deliver that same revolution to the additive industry. This is something that’s not lost on some of the 20 leading AM hardware vendors who’ve joined Dyndrite’s Developer Council, either eager to learn about, or develop new solutions and or standards that help them break free of legacy solutions and formats whose time has come to an end.
One new Council initiative, critical to bridging the OEM islands is the development of usable standards. First and foremost, Tool Pathing. What if your toolpathing data, created on one metal system, could be instantly reused on your different metal system, with enough process control to quickly deliver parts to the same quality, accuracy and repeatability? What if new standards enabled the development of applications in a secure ecosystem that simply worked?
It’s one thing to be able to prepare a build in less than 60 seconds with Dyndrite but the wider, broader effects that Dyndrite offers could make additive fully accepted – along with those production grade speeds, you add automation, scalability, and standards. To relate back to the AMFG Landscape graphic above, the vision of Dyndrite is to be the white space around all the groups - the glue that holds them all together.
With Dyndrite the additive industry stands a chance to be mainstream – not the bratty, red-haired step-child of mass production that it currently is. And I want to be part of that evolution of the industry.
This is why I joined Dyndrite.
Find out more on this topic by attending Dyndrite Developer Conference 2021, April 20-21 (virtual event)
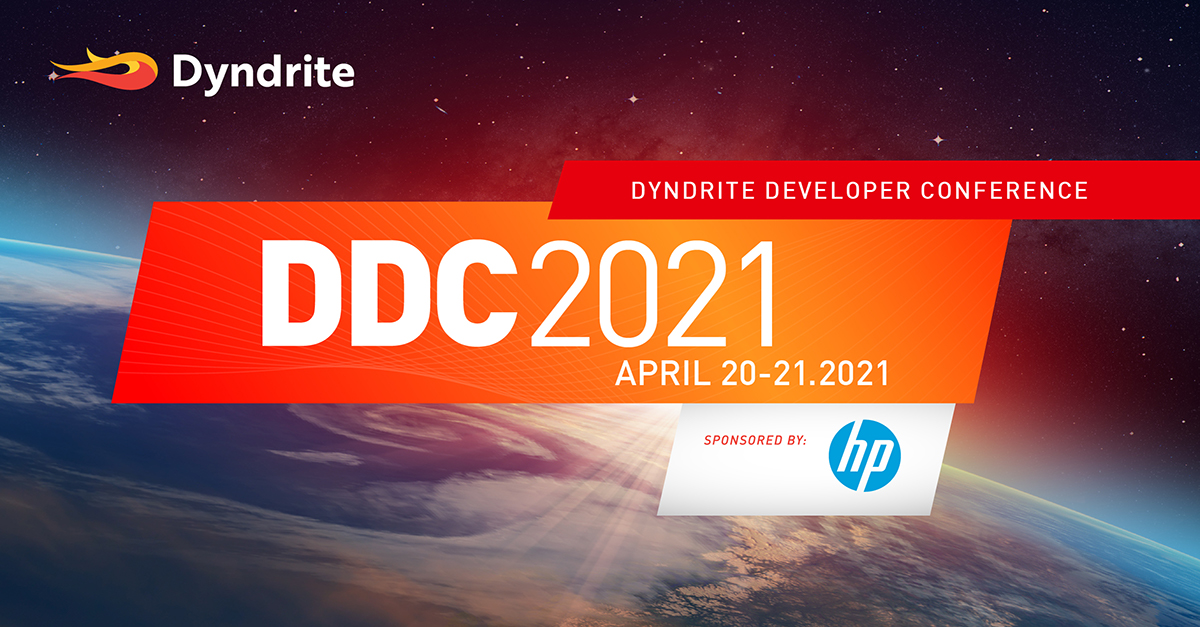