Dyndrite and Impossible Objects Speed 3D Data Preparation of Carbon Fiber Additive Parts by 10 times
● Automated, GPU-based, CAD-to-Print process in CBAM improves productivity and significantly lowers operational cost ● Advanced, automated nesting routines optimize Build Block utilization, lowering cost per part and improvements in material usage ● Rules-based process reduces failed builds and advances repeatability and part quality
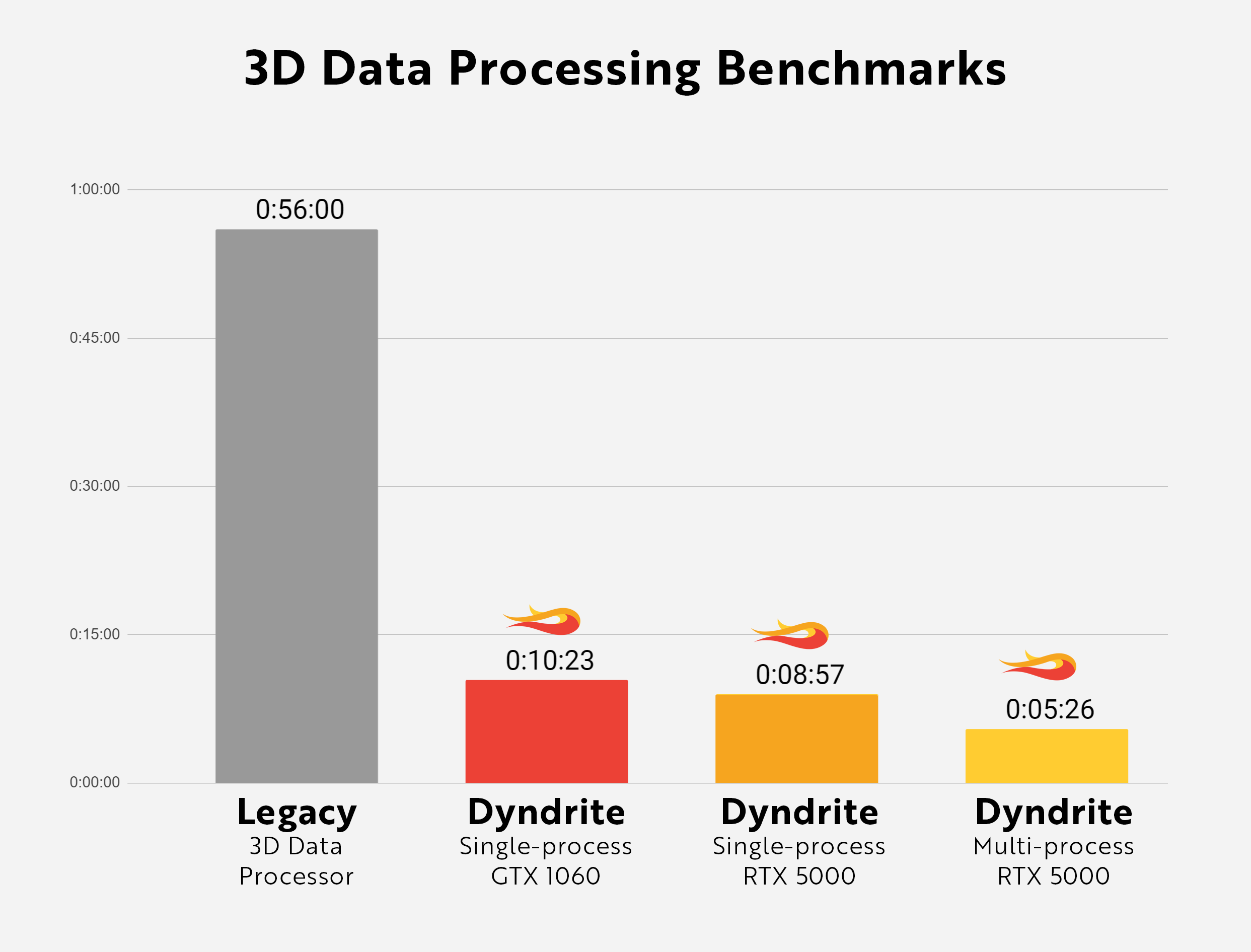
Seattle, WA., Sunday, September 12, 2021. — Dyndrite™, providers of the core Accelerated Computation Engine used to create next generation digital manufacturing hardware and software, and Impossible Objects, a 3D printer and materials company pioneering advancement of composites in additive manufacturing, today announced initial results of a joint project that speeds build preparation of 3D printed carbon and fiberglass composite parts by ten times.
Impossible Objects’ Rules-based Automated Masking Packing and Slicing software project, or ON-RAMP, powered by Dyndrite, fuses the multi-threaded, GPU-accelerated, Python-based Accelerated Computation Engine from Dyndrite with Impossible Objects’ proprietary software to drive its unique CBAM process. Composite-Based Additive Manufacturing – or CBAM – is a unique proprietary process designed to produce carbon fiber and fiberglass parts paired with Nylon and PEEK. It is designed to deliver production parts automatically, outshining hand layup production times while being 60% lighter than traditional parts.
“The improvement to overall workflow is remarkable. Manual build prep is reduced from 3 hours to a few minutes with automation, and 3D data processing benchmarks go from 56 minutes to 5 minutes, meaning that the entire 4 hour process is now completed in less than 10 minutes,” said Len Wanger, CTM, Impossible Objects. “Dyndrite is revolutionizing the user experience in the production of CBAM parts. The focused APIs, CAD import capability, combined with GPU-based processing of voxel data, plus Python automation, deliver cumulative benefits to the entire CAD to CBAM print workflow. As quickly as 2 weeks into the project we realized a huge time savings, and suspect this is just the tip of the iceberg.”
Driving Towards Serial Production With Additive Manufacturing
ON-RAMP Powered by Dyndrite, delivers an automated CAD-to-print workflow for Impossible Objects’ CBAM production process. Automation provides numerous benefits, including much faster processing of 3D data while reducing tedious manual labor, automated nesting that optimizes build space and minimizes scrap, and customizable workflows that allow significantly faster time to first part. Additionally, automating best practice design rules on build blocks allows the embedding of QA/QC data tracking for improved traceability and a reduction in part error rates. Finally, Dyndrite’s ability to quickly process very large 3D datasets streamlines the entire process.
“The last 30 years of software development for additive has been a failure due to fundamental issues and problematic philosophy,” said Harshil Goel, CEO and Founder, Dyndrite. “We are working to deliver software that speaks directly to making serial production a reality with additive manufacturing. This is the most important initiative for the next 30 years of additive. This is your time to become part of it.”
ON-RAMP will be demonstrated at the RAPID + TCT 2021 at the Impossible Objects booth # E8237 and Dyndrite at Booth# E7219.
“The number one factor preventing true serial production in additive is the software,” said Wanger. “With Dyndrite we are finding new ways to deliver much-needed repeatability and traceability, helping to overcome a key bottleneck in the production of composite parts. It’s like having an application engineer in a box --we are very excited.”
About Dyndrite:
Dyndrite’s mission is to fundamentally affect how geometry is created, transformed and transmitted on a computer. Our Accelerated Computation Engine (ACE), gives hardware and software companies the power, freedom and control necessary to deliver on the potential of digital manufacturing.
The Dyndrite Accelerated Computation Engine (ACE) is the world’s first multi-threaded, GPU-accelerated Geometry Software Developer Kit (SDK). Accessible via both C/C++ and Python interfaces, the Dyndrite Engine democratizes access to a hyper-scalable, geometry-agnostic set of digital manufacturing software tools that deliver eyebrow-raising performance. The company licenses the Engine to hardware, software and enterprise customers. Dyndrite’s team of mathematicians, computer scientists, and engineers exist to help our partners and licensees solve the toughest geometry, compute and automation problems so they can deliver production at scale. We aim to ignite their purpose.
Investors include Gradient Ventures, Google’s AI-focused Investment Fund and former Autodesk CEO Carl Bass. The company was founded in 2015 and is headquartered in Seattle, WA. Dyndrite was named a World Economic Forum Technology Pioneer for 2021.
For more information visit: www.dyndrite.com
Dyndrite PR Contact
Rachael Dalton-Taggart
Connect with Dyndrite
LinkedIn: https://www.linkedin.com/company/dyndrite/
Twitter: https://twitter.com/dyndrite
Facebook: https://www.facebook.com/DyndriteCorporation/
Dyndrite is a trademark of Dyndrite Corporation. All other trademarks and registered trademarks previously cited are hereby recognized and acknowledged.
About Impossible Objects
Impossible Objects is a 3D printer and materials company pioneering advancements in the additive manufacturing and composites manufacturing industries. Based on years of research and development, our composite-based additive manufacturing technology (CBAM) is an entirely new process that is fundamentally different from conventional additive manufacturing technologies.
Our CBAM process is designed specifically for composites. It produces parts stronger than other additive manufacturing technologies, faster than traditional composite methods, with more design freedom, and a broader selection of materials, including carbon fiber and fiberglass paired with Nylon and PEEK. And we’re just getting started. Our goal is to produce the world’s strongest additively manufactured composite parts, rivaling hand layup materials, at injection molding speeds.
For more information visit: https://www.impossible-objects.com
Dyndrite is a trademark of Dyndrite Corporation. All other trademarks and registered trademarks previously cited are hereby recognized and acknowledged.