2020 Will Mark a Turning Point in Additive Manufacturing.
Innovation in additive manufacturing hardware and materials in the last decade has been nothing short of phenomenal: an industry that was ‘good enough’ to do rapid prototyping, but nothing more, 20 years ago, has evolved into a thriving market that is providing certified parts for planes, satellites, energy infrastructure, automobiles and medical implants.
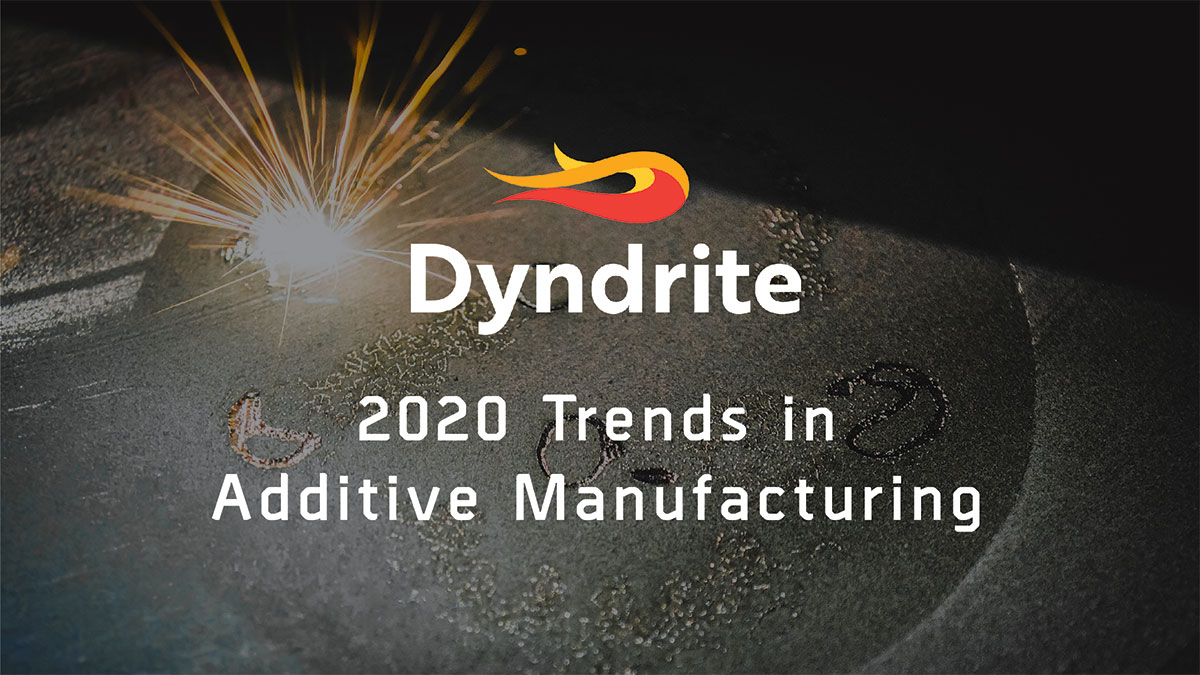
by Harshil Goel,Founder and CEO of Dyndrite.
The technology has arrived onto the manufacturing shop floor and is established as an essential tool in the design-to-production value chain.
Yet additive manufacturing remains constrained: quality issues, lack of compliance to six sigma repeatability, speed and throughput has made scaling difficult, especially as compared to traditional manufacturing processes. Every day additive manufacturing systems are engineered to be faster, more accurate and build more robust parts but are prevented from achieving maximum quality, repeatability, speed and scale by the very tools, file formats and software on which the work is based. The truth of the matter is, the hardware we use has outpaced the software that drives it. Call me biased, but I strongly believe 2020 is the year when software finally catches up, and leaps ahead. There are five key trends that I see happening:
Trend 1: Your 3D Printer is Becoming a 3D Printing Supercomputer
As 3D printer build sizes, resolution, precision and accuracy increases, so too the amount of data needed to drive the process. OEMs such as HP cite 3D file sizes of more than 4.5 terabytes for its MJF 3D printers – and these have a build size of 380 x 284 x 380 mm. If that build volume is increased by 50%, that file size will increase by a factor of 3.375 (1.5^3) or a whopping total of 15.2 terabytes. Using legacy or CPU-only software solutions to handle this amount of data has become untenable. This is about to change.
Video: HP's, SVP and Global Head of Software and Data, 3D Printing and Digital Manufacturing, Ryan Palmer, discusses driving scale and differentiated value through customization.
GPUs (Graphics Processing Units) are incredibly powerful, flexible, scalable and affordable architectures. Unfortunately, outside of rendering pretty pictures, most go unused in computational geometry. Employing the GPU’s data handling and computing power in the manufacturing process means that additive professionals can have power to deal with massive file sizes both on a computer and in a 3D printer. Putting an NVIDIA GPU into a 3D printer means bringing EDGE computing power at the point of manufacture – a preference for complex manufacturing instructions. In other words, you don’t need terabytes of manufacturing data per build, just the instructions on how to generate the parts, which can now be computed in the 3D printer.
Trend 2: Users are Gaining Greater Process Control Over Active Additive Production
Video: Ravi Kunju, Senior Vice President, Strategy and Business Development, Simulation Driven Design at Altair discusses how simulation driven design can apply to different manufacturing processes.
In-situ process monitoring and feedback is a developing area, mainly with metal PBF (Powder Bed Fusion). But as users start to expect more process control so they need more sophisticated tools. 2020 will see the rise of ‘feed forward’ applications that use both feedback systems as well as ‘feed forward’ systems that combine the powers of simulation software, such as from new Dyndrite Developer Council members, Ansys and Altair, and the 3D geometry kernel to adjust the print parameters during the build.
Video: Ansys' Director of Additive Manufacturing, Brent Stucker, shares how data-driven decision making can drive business value.
Combine this with the GPU computing power in your 3D printer and there is now a sophisticated 3D printing process, delivering fewer failures, better part quality and smarter material usage.
Trend 3: Toolpathing in Additive is Getting More Sophisticated
Once additive experts have greater visibility and control over the 3D print process, it is only natural that there will be a need for greater control over the toolpaths - more granular and real-time control of laser exposures, speeds and material feeds.
3D printing OEMs have started to adapt to this expectation, with EOS and Renishaw now exposing some print APIs to key customers and companies such as Aconity and Open Additive delivering highly configurable metal additive systems. To support this effort, The Dyndrite Developer Council has also formed a Toolpath Working Group, with participants such as SLM, to address what tools users want and need. As additive engineers become more sophisticated in their search for better part production, so must the software they use be responsive to their needs.
Video: Rüdiger Herfrid, Product Manager at EOS, shows how their platform can integrate with various CAD programs and looks forward to collaborating with Dyndrite this year.
Trend 4: Production Engineers Will Start to Abandon STL File Formats
It is truly amazing that the STL file format has existed as a standard for more than 30 years. As a tessellated approximation of a 3D CAD design it was fine for rapid prototyping, but lacks the robustness required for production-grade additive. Even more recent developments in file formats such as AMF and 3MF use the same geometric philosophies as STL, tessellated triangles - representations that explode data, cripple computers, 3D printers, and frankly, the industry.
Additionally, upon conversion, STL files often need to be repaired, destroying production momentum. They deliver pathological inaccuracies and by their very nature are an inherent disconnect from what the 3D printer is built to deliver - prints at the resolution of the machine, not the resolution of a tessellated approximation. As companies like Adobe figured out with Postscript® in the 80s, why would you even print fixed-polygonal data if your machine were capable of printing higher order geometries, such as splines? Being able to bypass STL formats in the build preparation and printing process fundamentally improves the quality, speed of build, and the ability to produce bigger and more complex parts accurately.
Dyndrite’s new 3D geometry kernel for additive manufacturing uses the original mathematical representation (B-spline, NURBS, and B-rep data) to deliver better additive tool paths and thereby 3D printed parts. It avoids ‘data-bloat’ by not relying on millions of triangles to define a print. It builds quality in a printed part by having tool paths defined by splines. This means improved repeatability and improved production speeds by eliminating the momentum-dissipating step of needing to repair the STL.
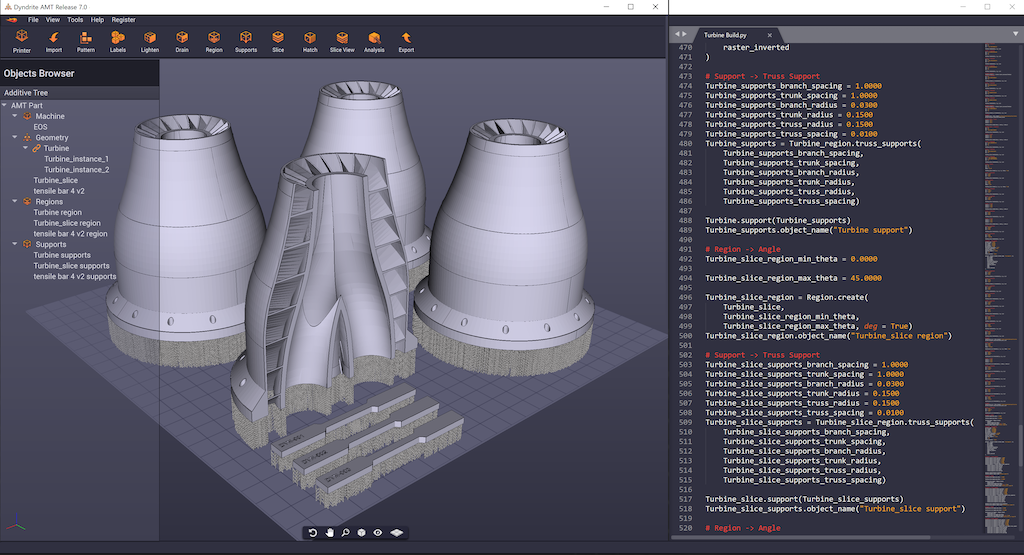
Trend 5: The Most Important Change is Happening in the People, not Machines
Most predictions are typically about hardware, materials and software. But I think the most interesting and fundamental evolutionary change is about the people using them.
As Shawn Hopwood, Dyndrite’s Chief Marketing Officer often states, “Technology doesn’t replace people. People who leverage technology replace the people who don’t”. There is a demographic shift going on within design and manufacturing. Today, engineering students are required to have software coding experience, and many engineers have been curious enough to delve into self-learning for coding using the many online resources available.
Powerful languages such as Python make programming accessible to just about anyone, even elementary school students. Having the ability to quickly script a task, cobble together a repeatable workflow, or prototype an app will bring tremendous new efficiency and opportunity to the industry, especially as people begin to share. My favorite quote by Marc Andreessen is that ‘Software is eating the world.’ And it is: and you better have some people on your team that can code some of it.
Again, I’m biased, but I believe 2020 will be remembered as a turning point in additive manufacturing, where both technicians and OEMs gain more power, freedom, and control over the production process and the software that drives it.
Find out more on this topic by attending Dyndrite Developer Conference 2021, April 20-21 (virtual event)
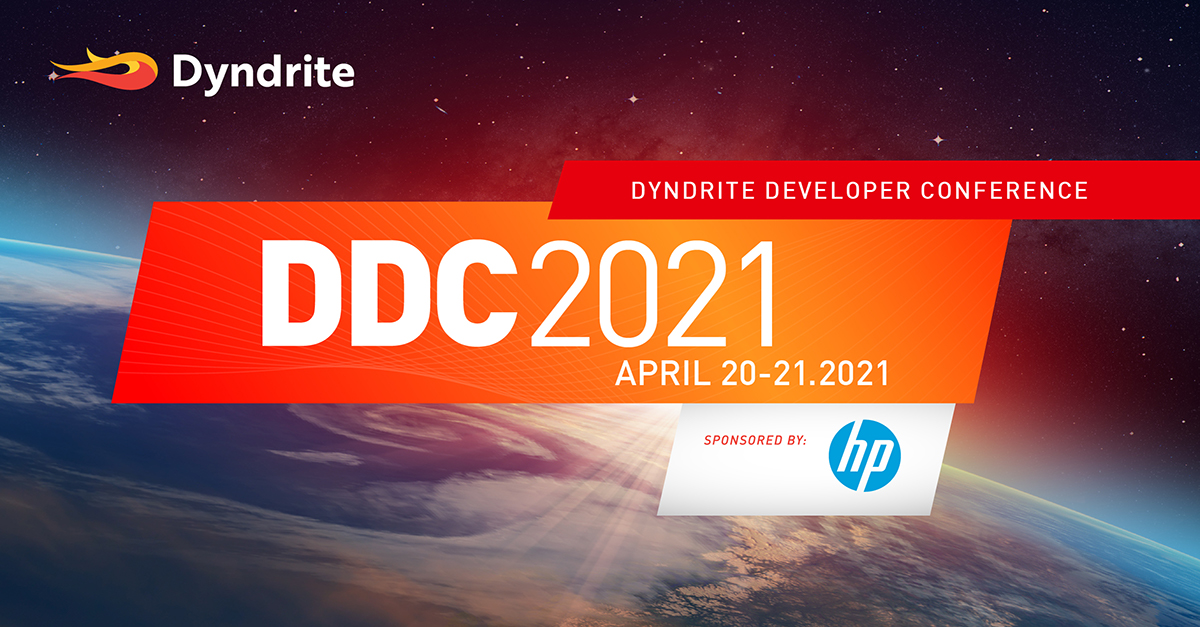